
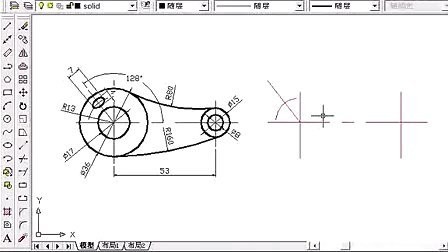
While working with clients of all sizes, we see different ownership levels and responsibilities when it comes to the production of custom products.
When it comes to custom designed products, some buyers will make sketches, mock-ups and computer aided design (CAD) files for the vendor to iterate on. The expectation is then for the manufacturer to do something called “design for manufacturing”. The need for design for manufacturing is because sometimes designs that are provided in CAD or 3D files are not manufacturable. Meaning, that at scale, it will not be cost efficient to produce.
For example there are certain techniques, design and materials that you may have envisioned for your product that may not align with the equipment that the factory has on hand or even the ability to build. In the event that the factory can produce your product to specification, you have to ensure that the goods are produced at a cost that will allow your business to profit.
When working with the suppliers, you should closely understand the product needs and the requirements to have it built. To be proactive, the best way to go about this process is to have your industrial designer collaborate with the factory in idea concept stages to understand the material choices, design constraints and manufacturing equipment.
Then, from there, work to develop the 3D file collaboratively with the factory’s engineers to produce a manufacturable file that will render profitable goods. This will help save time and money on the design. It will also allow tooling to be more efficient and successful. While doing this, also be aware that there will be multiple passes, changes to design files and iterations that will need to be organized, owned and reviewed.
With this in mind, it is important when you’re scoping the vendor that you clearly outline the intellectual property, MSA, confidentiality and statement of work prior to kick off. There should be clear expectations on ownership and what is prohibited. When working with your team to provide these supplemental documents, collaborate to understand risks and which responsibilities should be included. There will also be finalized documents like Bill of Materials, Design for Manufacturing (DFM), Drawings, Color Material Finish documents and more. Understanding who contributes to them, which are the finalized versions, who owns the document and has access to them are extremely important to the success of your business.
In advance, make it very clear which process of design you’re going to be utilizing, outlining the relationship with your factory partners and have clear legal documentation listing ownership and contributions. Working with factory partners is an extremely rewarding, but intricate process. For support on designing, developing and bringing products to market – reach out to Victure Group!
For product sourcing, you’re suggested to join the following LinkedIn groups
China Sourcing- China Sourcing, Networking, Import, Export, Trading, Manufacturing | Groups | LinkedIn
Green Economy- Sustainable, Circular, Green Economy Forum, Networking, Supply Chain | Groups | LinkedIn
Vietnam Sourcing- Vietnam Sourcing, Networking, Import, Export, Trading, Manufacturing, Supply Chain | Groups | LinkedIn
Indian Sourcing- India Sourcing, Networking, Import, Export, Trading, Manufacturing, Supply Chain | Groups | LinkedIn
Asia Sourcing- Asia Sourcing, Networking, Import, Export, Trading, Manufacturing, Supply Chain | Groups | LinkedIn
Gift and Premiums- Gifts and Premiums | Groups | LinkedIn
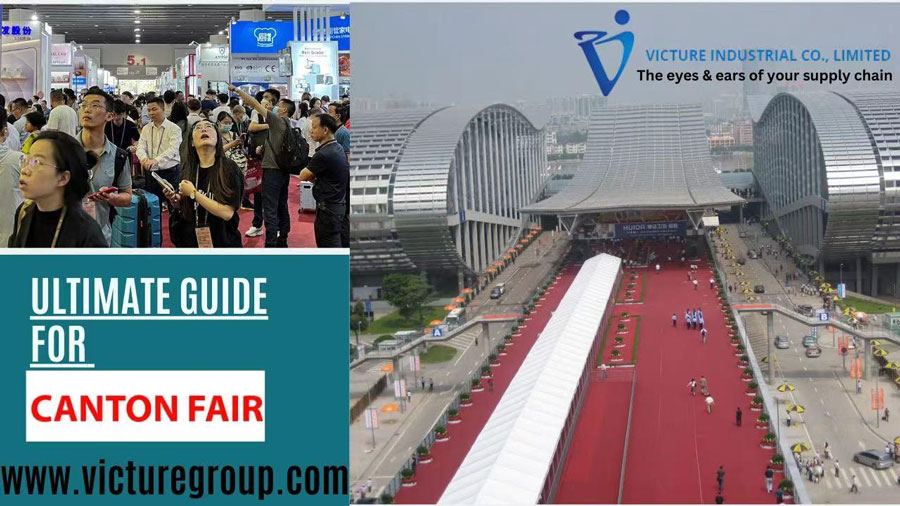
October 13, 2023
Ultimate Guide for Canton Fair TourLow and High Production
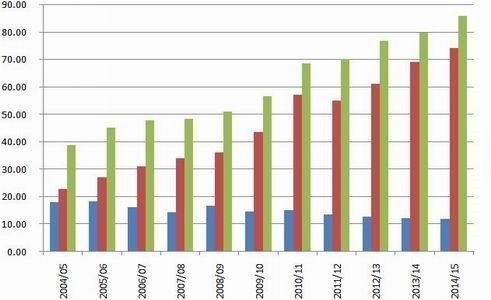
July 08, 2021
Low and High ProductionLow and High Production
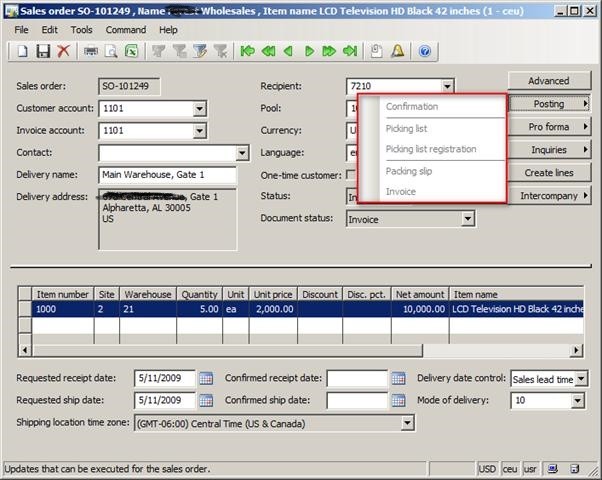
June 17, 2021
Order Volume ConsiderationsLow and High Production
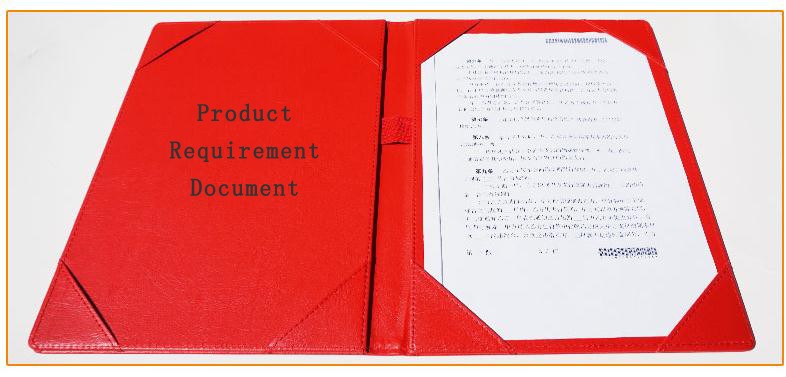
June 09, 2021
Product Requirement DocumentLow and High Production
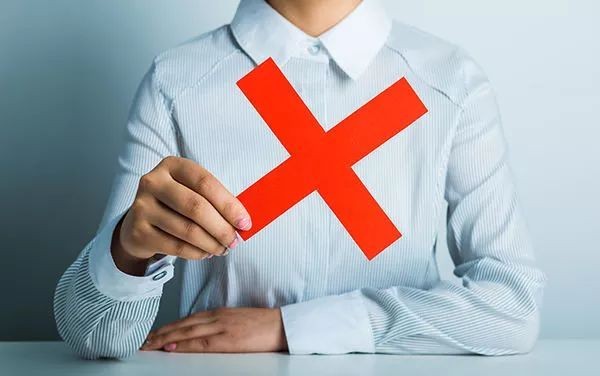
June 03, 2021
Mistakes When Approaching FactoriesLow and High Production